HRVS-DN
|
Digital, Heavy Duty, Medium Voltage Soft Starter - 2.3-15kV, up to 48MW
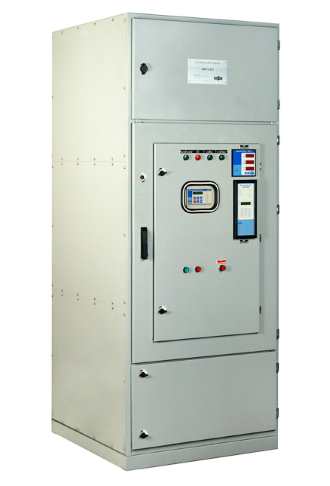 |
|
The HRVS-DN is heavy duty Medium Voltage Soft Starter, designed for Medium Voltage AC induction motors including Marine and Mining applications. The HRVS-DN’s sophisticated motor control technology ensures smooth acceleration and deceleration as it minimizes the effect of high in-rush current and mechanical torque shock. Advanced features including customizable starting curves, unique voltage measurements, flexible design and enhanced motor protection as well as a global track record make the HRVS-DN the starting solution of choice for Medium Voltage applications even under the most demanding conditions. |
|
The HRVS-DN’s flexible configuration is designed to meet requirements of new applications, retrofits and OEM customization. It is available with Marine approvals and with ProGear, a fully Type Tested Arc Resistant switchgear. |
|
|
|
HRVS-DN Digital Medium Voltage Softstarter
|
Advance Features |
 |
- Configurable starting & stopping characteristics
- Enhanced motor protection package
- User friendly setup and operation
- Multi-soft start and multi-soft stop
- Unique synchronous motor starting module
- Dedicated generator starting curve
- Pump and load control
- Advanced Electronic Potential Transformer (EPT) utilizing fiber optics for complete isolation between Low and Medium Voltage sections
- Partial Discharge test according to EN50178/625.1
- Direct Power Factor Capacitor connection
|
|
- 45-65Hz Auto-tracking frequency range
- Easy to conduct Low Voltage test
- EMC design and test
- Communication options: Modbus, Profibus, DeviceNet
- Compact 2-phase control configuration (optional)
- Data Logger – An Integraded current and voltage wave recorder at a sampling rate of up to 50kHz with advanced graphic software interface for remote waveform monitoring (optional)
- Multi-voltage and multi-current starting
|
|
|
Details
|
Switchgear options |
 |
Fully Type Tested, Arc Resistant, Medium Voltage Soft Starter Switchgear
Metal enclosed cabinets manufactured according to IEC standard 62271-200. Adhering to the highest safety standards, Solcon’s ProGear is designed for uncompromising protection and performance. |
|
- Rated: up to 12kV, 1250A
- Internal Arc Test 31.5kA/1sec, IAC: A-FLR
- Short-time withstand current 31.5kA/3sec
- Dielectric Test – Power Frequency 28kV 60sec – Impulse voltage 75kV
- Temperature Rise Test
- IP54 Protection Degree
|
|
Starting and Stopping |
 |
- Soft start and soft stop
- Current limit
- Pump control characteristics
- Torque contro
|
|
- Dual adjust
- Pulse start (kick start)
- Tacho feedback
|
 |
|
|
Integral Protection |
 |
- Bypass open
- Under Voltage
- Under current
- Too many starts
- Current unbalance
- Phase sequence
- Maximum start time
- Electronic overload
- Instantaneous over current 100-850%
- Time over current
|
|
- Ground fault
- Over Voltage
- Number of starts
- Under/over frequency
- External fault
- Power ON no start
- Thermal modeling
- Phase loss
- Shorted SCR
- Over load class trip
|
 |
|
|
Control |
 |
- Closed control circuit through current measuring
- Multi-function programmable I/O’s
- Opto-isolated control in- and outputs
- Transformer 8A/250V
- Analogue outputs
|
|
- Analogue inputs
- Modbus / Profibus
- Touchscreen
- SPS
|
 |
|
|
Applications |
|
|
 |
Marine and offshore |
|
Industrial |
 |
- Water and ballast pumps
- Refrigeration chillers and compressors
- Hydraulic pumps and power packs
- Thrusters
- Main propulsion motors
- Cargo pumps
- Generator ready – auto frequency tracking
|
|
- Pumps
- Compressors and chillers
- Fans and blowers
- Centrifuges
- Hydraulic systems
- Conveyors
- Mills, crusher, shredder
|
|
|
|
|
Models | 2.3-15kV, 60-18,000A
|
|
Main Voltage (kV) |
Rated Current (A) |
Moto kW(kW) |
2.3 |
60 |
200 |
110 |
360 |
200 |
660 |
320 |
1,060 |
400 |
1,330 |
500 |
1,660 |
600 |
2,000 |
700 |
2,300 |
800 |
2,660 |
1,000 |
3,330 |
3.3 |
60 |
280 |
110 |
520 |
200 |
950 |
320 |
1,530 |
400 |
1,910 |
500 |
2,390 |
600 |
2,850 |
700 |
3,325 |
800 |
3,820 |
1,000 |
4,780 |
|
|
Main Voltage (kV) |
Rated Current (A) |
Moto kW(kW) |
4.16 |
60 |
360 |
110 |
660 |
200 |
1200 |
320 |
1930 |
400 |
2410 |
500 |
3010 |
600 |
3610 |
700 |
4,210 |
800 |
4,820 |
1,000 |
6,030 |
6.6 |
70 |
670 |
|
140 |
1,340 |
|
250 |
2,390 |
|
300 |
2,870 |
|
400 |
3,820 |
|
500 |
4,780 |
|
600 |
5,736 |
|
700 |
6,740 |
|
800 |
7,650 |
|
1,000 |
9,570 |
|
1,200 |
11,500 |
|
1,400 |
14,000 |
|
1,600 |
16,000 |
|
1,800 |
18,000 |
|
|
|
|
|
Main Voltage (kV) |
Started Current (A) |
Moto kW(kW) |
10 |
70 |
1,020 |
140 |
2,040 |
250 |
3,650 |
300 |
4,300 |
400 |
5,800 |
500 |
7,250 |
600 |
8,700 |
700 |
10,150 |
800 |
11,600 |
1,000 |
14,500 |
1,200 |
17,400 |
1,400 |
22,000 |
1,600 |
25,000 |
1,800 |
28,000 |
|
|
Main Voltage (kV) |
Started Current (A) |
Moto kW(kW) |
11 |
70 |
1,100 |
140 |
2,200 |
250 |
4,000 |
300 |
4,800 |
400 |
6,400 |
500 |
8,000 |
600 |
9,600 |
700 |
11,200 |
800 |
12,800 |
1,000 |
16,000 |
1,200 |
19,200 |
1,400 |
22,400 |
1,600 |
25,600 |
1,800 |
28,800 |
13.8 |
70 |
1,400 |
140 |
2,800 |
250 |
5,000 |
300 |
6,000 |
400 |
8,000 |
500 |
10,000 |
600 |
12,000 |
700 |
14,000 |
800 |
16,000 |
1,000 |
20,000 |
1,200 |
24,000 |
|
|
|
|
*Higher streams and achievements on request |
|
Approvals
|
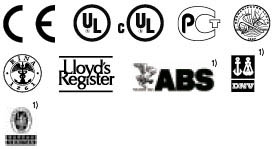 |
|
1) Case by case |
|
Current limit
|
The voltage increases linearly from the “Initial Voltage“ pre selected point. If the adjusted “Current Limit” is reached, the voltage will stop ramping and remain at its level until the current is reduced below the adjusted “Current Limit“ level. In that case ramp up time is prolonged until the current has reduced below “Current Limit” level |
|
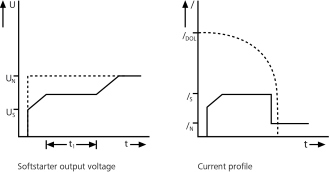 |
|
Although the current is limited the motor provides suitable torque to accelerate the driven load and reach “End of acceleration”. If the motor torque does not exceed the load torque the motor will not start. In the so rare cases severe damages might occur to the motor and starter. |
|
|
|
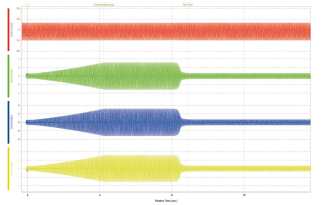 |
|
The oscillogram shows, the soft starter providing a smooth and stepless current and voltage ramp to the motor. The voltage ramps up until “Current Limit” is reached. After the motor is at nominal speed, the current will decrease, to the nominal motor current. |
|
|
Pump control
|
Our digital Soft Starters line of products provide an advanced microprocessor based control algorithm, enabling the sophisticated pump control feature. The motor torque is continuously monitored to eliminate peak torque from stressing the motor, pump and pipe system. These soft starters provide 3 field selectable pump control algorithms. |
|
Pump and special load control |
Two major problems are associated with starting and stopping of pumps. |
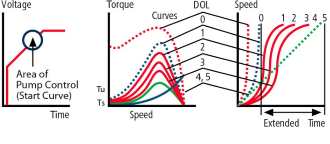 |
|
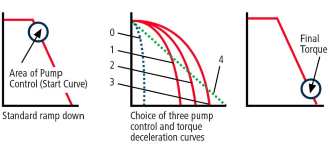 |
|
|
|
Over-pressure during starting |
|
Water hammer during stopping |
The sharp increase of torque towards the end of acceleration can cause high pressure and damage the pipe system. The pump control enables selection between three voltage ramp-up curves as well as torque curve to reduce peak torque. Current ramp is available for special loads. |
|
During soft stop, when voltage is decreasing, motor torque may fall below load torque causing abrupt stalling instead of smoothly decreasing speed to zero. This creates the “water hammer” phenomenon (resulting in a loud noise and damage to the pipe system). The pump control algorithm enables selection between three voltage ramp-down curves or torque curve pre venting stall condition and eliminating water hammer. |
|
|
|
Digital
|
|
Communication RS 485
|
- Illuminated LCD with 2 lines of 16 characters each
- Selectable languages: English, German, French or Spanish (aditional on request)
- The LCD indicates the motor current, fault descriptions and statistical data.
- The LEDs provide a quick status indication. (control voltage on, motor soft start, motor on, motor soft stop, motor stop, fault)
- Easy settings by six clearly marked keys, user-friendly software with factory default parameters.
|
|
RS 485 with MODBUS or PROFIBUS protocol enable: |
|
- Remote (start, stop, etc.)
- Monitoring (motor current, faults, statistical data)
- Remote parameter setting
- Remote reset
|
|
|
Bypass
|
Internal bypass |
 |
- This reliable components bypass the power electronics after the motor is at speed.
- In addition the starters provide an auxiliary contact, allowing signaling of a successful motor start. Attention! Many of our competitors call these auxiliary relays “a bypass contact”!
- The bypass function reduces the heat dissipation and eliminates the EMC load of the system.
|